In the realm of modern manufacturing, CNC (Computer Numerical Control) technology has revolutionized the production process. Central to this technology are CNC inserts, which play a vital role in achieving precision and efficiency.
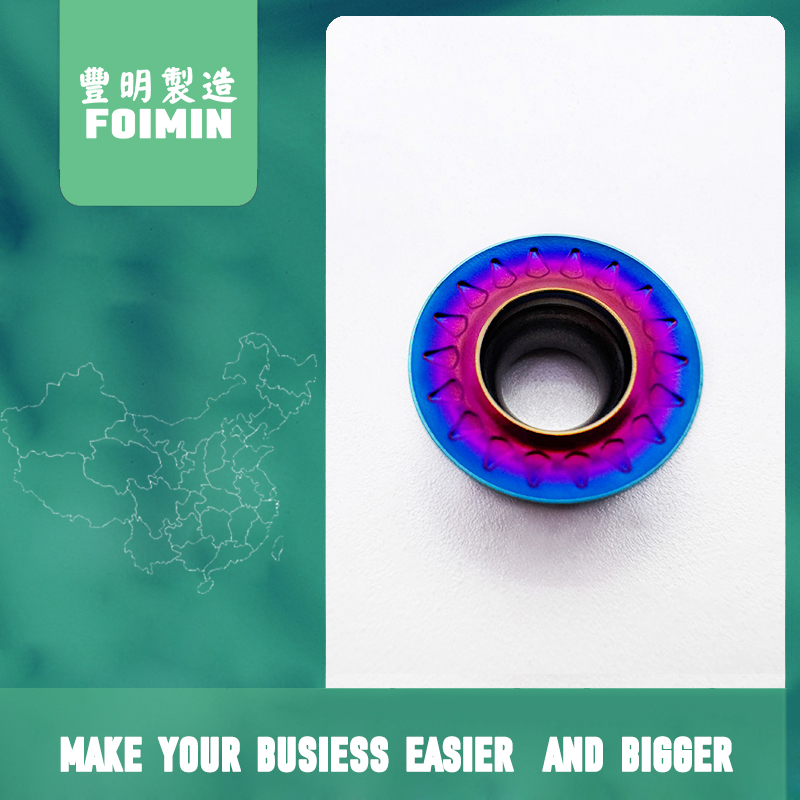
CNC inserts are cutting tools that are specifically designed to be mounted on CNC machine tools. They are available in a wide variety of shapes, sizes, and materials. The choice of the right CNC insert depends on several factors such as the type of material being machined, the desired surface finish, and the cutting parameters.
One of the key advantages of CNC inserts is their versatility. They can be used for various machining operations including turning, milling, drilling, and threading. For instance, in turning operations, different types of inserts can be used to create cylindrical shapes with high accuracy. In milling, inserts enable the creation of complex profiles and cavities.
The material of CNC inserts is crucial. Carbide inserts are popular due to their hardness and wear resistance. They can withstand high temperatures generated during cutting and provide a longer tool life. However, other materials like ceramic and cubic boron nitride (CBN) are also used for specific applications. Ceramic inserts are suitable for machining hard and brittle materials such as cast iron and hardened steels at high speeds. CBN inserts are even more hard and are ideal for extremely hard materials.
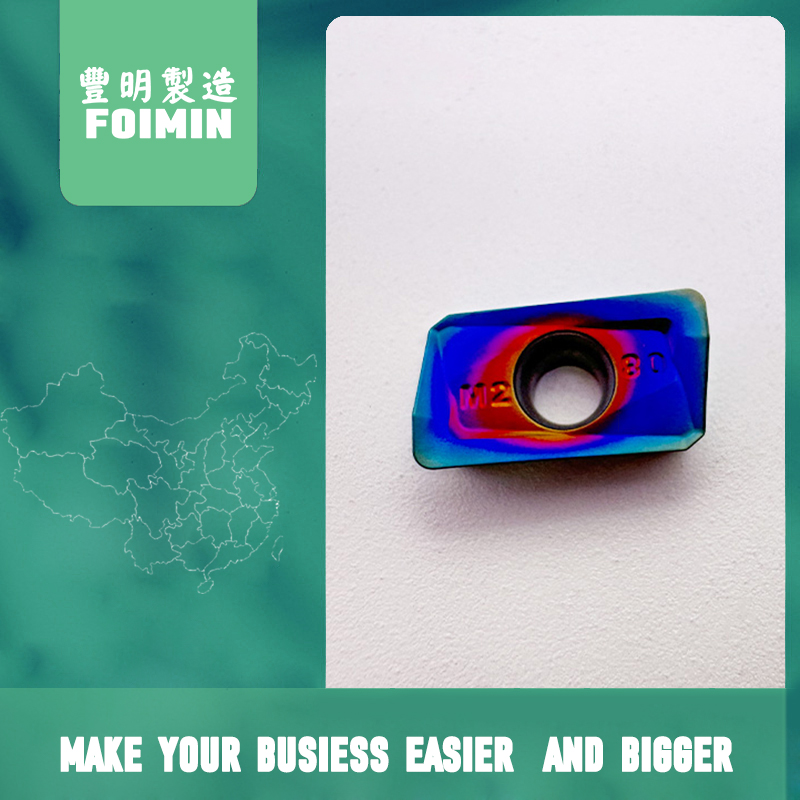
The geometry of CNC inserts also impacts their performance. The rake angle, clearance angle, and cutting edge geometry are carefully designed to optimize chip formation and removal. A proper rake angle helps in reducing cutting forces and improving surface finish. The clearance angle ensures that the insert does not rub against the workpiece, thereby reducing heat generation and tool wear.
In recent years, there have been significant advancements in CNC insert technology. Coating technologies have emerged as a major breakthrough. Coatings such as titanium nitride (TiN), titanium carbonitride (TiCN), and aluminum titanium nitride (AlTiN) are applied on the surface of inserts. These coatings enhance the hardness, lubricity, and oxidation resistance of the inserts. They reduce friction between the insert and the workpiece, allowing for higher cutting speeds and feeds. This not only improves productivity but also results in better quality of the machined parts.
Another area of development is the design of insert holders. The holders are engineered to provide better clamping force and stability. This ensures that the inserts remain in position during high-speed machining operations and minimizes the risk of vibration and tool breakage.
Moreover, the advent of intelligent CNC machines has enabled real-time monitoring of the cutting process. Sensors can detect the wear and tear of CNC inserts and adjust the cutting parameters accordingly. This predictive maintenance approach helps in reducing downtime and increasing the overall efficiency of the manufacturing process.
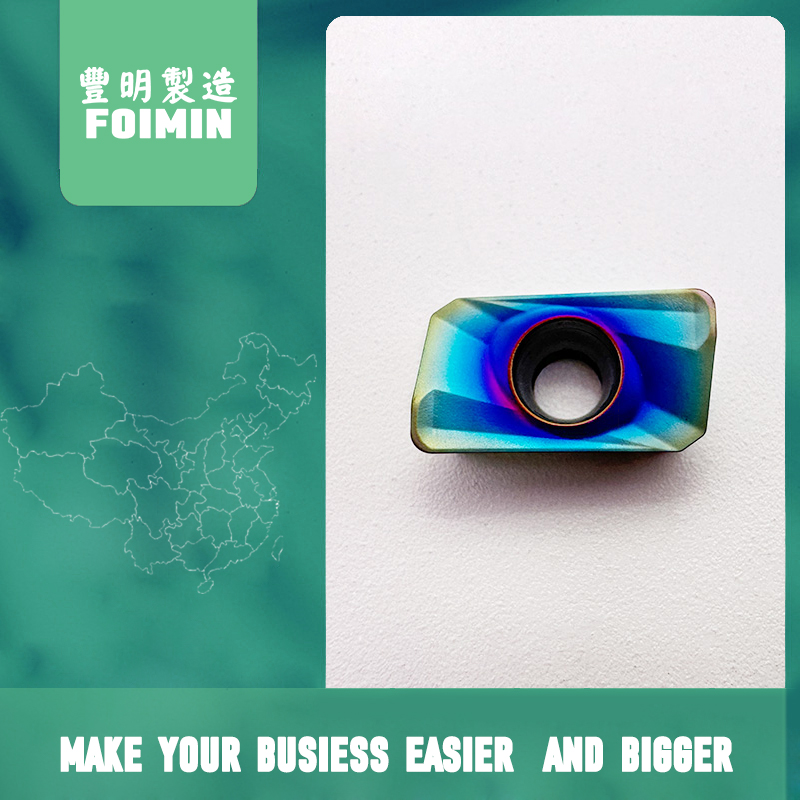
In conclusion, CNC inserts are the unsung heroes of modern manufacturing. Their continuous evolution in terms of materials, geometries, coatings, and integration with intelligent machining systems has paved the way for enhanced productivity, precision, and quality in the production of a wide range of components. Whether it's in the automotive, aerospace, or any other manufacturing industry, CNC inserts will continue to be a cornerstone of efficient and accurate machining operations.